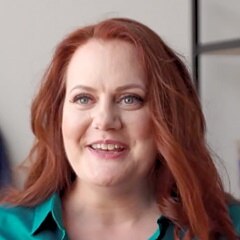
14-Day Learn to Sew Series - Needles and Thread
Katrina WalkerDescription
Let's talk about needles and thread. Needles and thread are two of the most important components in successful sewing. But strangely enough, they don't get talked about very much, so I want to make sure that you have a good basic understanding of how needles and threads work together to make your sewing successful. I'm going to start with needles. And I have the wonderful gift of a giant needle here from my friends at Schmetz so I can show you a little bit more, firsthand, the anatomy of how a needle is put together.
And then hopefully when I talk about needles, it'll make more sense. Alright, so, most sewing machine needles, this one is quite huge, I think it was a sale, one thousand, or, it's a mock-up obviously. But most sewing machine needles for our regular sewing machines have a flat back on them. So this part always goes to the back of the machine, so pointing away from you. We're just gonna start at the end there.
And this course is Schmetz. Now we get down to, this is called the blade. The main part of the needle is called the blade. And running down the blade is the groove. And the groove, this is where your thread actually lays, and so the groove protects your thread as it passes through your fabric, and also guides it down to the eye of the needle.
So this is the eye of the needle and then of course we get down into the point and the tip of the needle. Now if I flip this over to the back just above the eye is this little indent here, this little groove, and this is called the scarf of the needle, so behind the eye, just above it, is the scarf, and this scarf shape helps to influence how the stitch forms with the bob and thread. Alright, so, it helps to make that connection, make that lock-stitch happen. So all of these things, you know, the groove, the blade, the tip, the point, the eye, all of these things are part of how a needle actually works. So, let's start with looking at some needles for woven fabrics.
So needles for woven fabrics all tend to have more of a sharp point to them, or a sharper point to them. Now, I have several needles here that we can look at and I'm gonna start with kind of the universal. So the universal is the least sharp of my needles and the universal has a slight ballpoint. It's called a universal because it's kind of a jack of all trades when it comes to needles. The universal needle can be used for moderately woven fabrics, that is, fabrics that aren't too tightly woven, and it can be used on knits that aren't real sensitive, aren't real delicate, so it's again, it's universal for that reason.
It has just a slight bit of a ballpoint around the tip to it. Then we get into more specialized needles, now, needles will have names that kind of give you a hint as to what you're gonna use them for. For instance this is a quilting needle, and this quilting needle has also a fine, slightly rounded point, and it's very good for piecing cotton. Okay, piecing cotton fabrics. And it's designed to create nice, straight stitches, so it's excellent for piecework.
And just the name right there, quilting, should give you a hint of what you use it for. Now, we get into more specialized needles. Like this is called a microtex needle. And a microtex needle also is called a sharp needle, because the microtex needle has an extremely fine, fine, sharp point on it, very, very sharp, and that is because it is designed to sew with really tightly woven fabrics like microtex fabrics, again the name gives you a hint what it's for, I use microtex needles on silk a lot. Because a lot of silks are very tightly woven, So that extremely small point helps you get in between the fibers in the weave structure, and helps your stitches to form correctly, and not skip.
So that's what the microtex is for. Now, similar idea, but a completely different type of needle, is the denim needle, now, denim needles are for working with heavy fabrics. So again the name of the needle pretty much gives it away. And when you're working with a heavier fabric, you need to make sure your needle is strong enough to actually go through and not flex. So, what'll happen is, if you're using the wrong type of needle on denim, or a type of heavy fabric, when the needle strikes the fabric, it'll actually bend a little bit.
And that is called needle deflection. And when needle deflection happens, the stitch will look crooked, or it might even skip stitches, so this is something that is really important to emphasize, is that using the correct needle, will impact your sewing appearance. If you're using the wrong needle, or a dull needle, you do need to change your needles regularly, I change my needles usually at the start of every project or every eight hours. If I'm sewing on something like silk, or polyester, those types of fabrics will dull your needles faster, and therefore you need to change them even sooner. If you hear a popping sound, or kind of a thudding sound when your needle hits the fabric, it's dull.
You need to change your needle. I can tell across the room if one of my brighter machines is getting dull. I can hear it, you need to switch it out. So the denim needle has a reinforced blade, remember when we looked at the anatomy of our needle, a reinforced blade that helps keep it from bending. Helps it to go through that real thick fabric, helps it to penetrate and be able to form nice, straight stitches.
Now a similar type of needle, in terms of being designed to create beautiful stitches, is the topstitch needle. The topstitch needle has a specially designed eye and groove and so it's actually meant to be used with some of our heavier threads, and to allow them to pass through the eye of the needle more smoothly, without shredding your thread or similar. So the topstitching needle also has a little bit of a sharper point to it, than say, the universal, so it helps it to go through all those layers when you're topstitching. Just a really handy needle. I actually use topstitch needles a lot, because I like the way that they stitch.
But the embroidery needle, this embroidery needle, and of course I do a lot of machine embroidery so I use a ton of these as well. Embroidery needles also have a specially designed groove and eye, that helps to, again, protect some of our delicate embroidery threads, protect things like our metallics and such. Embroidery causes the thread to go through the fabric very fast, and so, the thread needs more protection. So this eye has a different shape to it. Now, this particular needle is also titanium coated.
Some needles are coated with titanium, some with chrome, there's different types of coatings, and so what the coatings do is, number one, they can help to reinforce the needle, make it a little bit stronger than just plain steel. But they also help to diffuse the heat. So when your needle goes through the fabric, very rapidly, and especially certain types of fabric, it gets hot. It heats up. I've actually burned my finger on a needle before.
I know that sounds crazy, right? But, it happens. And if you're sewing with a thread that is made out of, say, plastic, or some kind of artificial thread, they can actually melt. You can actually have your thread break because it melted, because your needle got too hot. And so these coatings actually help to diffuse the heat so the needle doesn't heat up quite as quickly.
But mostly they tend to run longer and stay sharper because of the coating. That's the main reason most people will buy them but I think about the heat aspect as well. And so these are all good woven needles, but of course, if we want to sew on knits, we have special needles for those. And here's a couple different ones. Now there's a ballpoint needle, and a stretch needle.
Now, might be a little confusing, because the stretch needle is also a ballpoint. But, why a ballpoint? Ballpoint needles are also sometimes called jersey needles. Jersey knits tend to be more loosely knit, and the yarns can be damaged more easily. So, the ballpoint, instead of being a sharp point that's gonna push down through the fabric, it's going to actually encourage the yarns in the fabric to move aside for the needle.
So you're less likely to cut the yarns when it's penetrating through the fabric, and it just tends to make your knit fabrics a lot happier. Now the stretch needle is really interesting, now the stretch needle actually has a specially shaped scarf, so remember the scarf is that indent, that indent behind the eye of the needle. And so the scarf on the stretch needle is specially designed to help prevent skipped stitches. So it helps the bob and thread to hook up with the top of the needle thread more accurately, and so the stretch needle is really great for anytime you're sewing with anything that has a lot of polyurethane. Polyurethane also called spandex, or Lycra, is a trade name, a brand name, of polyurethane.
Anytime you have those type of stretch fabrics, this is going to help you to get better stitch formation. So, prevent skipped stitches. It's also great for fabrics such as Ultrasuede, when I embroider Ultrasuede, a lot of times I'll use a stretch needle. Because it tends to help skipped stitches. And so, it's a pretty awesome needle to have in your collection.
But we even have other specialty needles, and it goes on and on, there's so many different needles. I'm just gonna focus on some of the main ones. But for special effects, we also have things like twin needles. So, twin needles are great for making details such as pintucks, I like to use them to mimic the toptstitching on knit fabrics. So if you do a knit hem on a knit and you want that double needle look, you can use your twin needle to accomplish that.
Now, they have, of course, different types of needles that are put into a twin format. Like this is a stretch twin needle. So you're not stuck with just one type, there are specialty twin needles. And we even have triple needles, for getting some really beautiful effects with different threads and things. So, that just gives you a little bit of an idea of some of the different types of needles.
Now one thing to understand about needles in terms of choosing, I think you can understand the idea behind choosing a particular, say, size, or a particular type of needle, but actually it was the size I mean to say, how do you know what size to use? So when you're matching up a needle to your thread and you're trying to figure out what size to use you really do just want to look at, okay, how thick or how heavy is your fabric? And how thick or heavy is your thread? That will help determine what size the needle is. So, needle sizing, when we look at a package of needles, like this Schmetz topstitch needle, it's a size 80/12.
So, with a needle, the larger the number, the larger the needle is. So, size 80/12, this is a really nice size for just your general such stitching. For most medium weight fabrics, light to medium weight fabrics, and your standard sewing thread, an 80/12 is a nice size. I use 90/14s a lot as well. But that's a nice size.
If you're using really fine fabrics you might want to go down to a 70, or even a 60. I don't use 60s or 65s very often, only because they're difficult to thread. And so I tend to stick with a little bit larger just because it's easier for me to thread the needle. But they do go smaller. But an 80/12 is really a nice size and works for a lot of different projects.
Whereas when you get into your jeans, your denim needles and things, then you're gonna get up to, this is a size 110. And this is a very large needle. About the largest sized needle you're gonna see is a size 120. So 120/19, that's going to be about the largest home sewing needle you're going to see. Normally, you know, there may be an exception.
But 110 is very, very heavy. So if you're sewing through a lot of layers of denim you might consider a size 110 just to have that extra strength. But this is a really, really big needle. It would make a very big hole. And that's why I talk about matching the size to your fabric, you know, how large a hole do you need?
Your needle's only job is to make a big enough hole to pull the thread through. Right? So we go with the heavier needle if we need the extra strength. Otherwise go with a lighter needle, and you'll be happier. Now of course, that leads us to talking about thread.
Now when we talk about thread, there are so many different kinds. Just like with needles, the number of different kinds of threads is pretty much mind boggling. And so, the key here, the key really is to consider,, okay, what kind of effect do you want? How are you gonna use it? And we pretty much kinda tend to divvy up thread, I think it's easier to start by separating it out into the fiber type.
All right, so I'm going to start with polyester. Simply because, polyester really is, that's my workhorse. I like polyester thread because it's very strong, it's very smooth, you can buy it in a lot of different colors. It launders well. It's just, it's very strong.
And so, it won't let you down. So, polyester, and this is a 40 weight, and I'd better address that before I go too much farther. So with thread, it's the opposite of needles. Okay, so, with needles, the bigger the number, the heavier the needle. With thread, the bigger the number, the finer the thread, the smaller the thread.
I know, why couldn't they have just matched it up, right? Wouldn't that be nice? Like, okay, a size 100 thread uses a size 100 needle. No, it's completely the opposite, so it's important that you understand this. So this says 40 weight polyester.
Now a lot of polyester threads for just basic, generic sewing, are gonna be 50 weight. So they're just slightly finer than this. But 40 weight's a nice weight. Again, it's nice and strong, it shows up well if you want to do a little bit of decorative stitching with it. So, 40 or 50 weight works great for thread.
But polyester is pretty much my main workhorse for thread. Majority of my construction work is basically done with polyester thread. But, that being said, a lot of quilters especially like cotton threads. Here are a couple of specialty cotton threads. I don't do construction with cotton thread, because I predominantly do clothing.
And when you do clothing, cotton threads will rot over time. And I know this because I have very expensive store-bought clothes that I've had to basically reconstruct because there'd be cotton thread, I'm not sure why they'd use cotton thread but they did and it eventually started rotting out after several washes. So, don't use cotton thread for clothing. That's my request. Unless it's something that isn't going to be washed very often or only hand washed.
But anyhow, there's no reason not to use cotton for things like, a lot of quilters like the way cotton thread looks for piecing. They like the way the stitches look in cotton thread. And that's completely valid. You will need to clean your sewing machine out more often, because it does tend to be linty, so do be aware of that. But these are two threads I like a lot for topstitching.
So again, topstitching or embroidery, a lot of special effect. And so one of these, the orange one, is 12 weight. So remember the smaller the number, the bigger the thread. So basically thread is by weight. So it's some sort of distance.
Now does that mean a 50 weight thread, you know, it's literally twice as heavy as a 100 weight. I'm not sure, but it could be. But I think you can see, just, even in my hand, the difference in weight between this 30 weight in the aqua, and the 12 weight in the blue. 12 weight really is a nice, nice weight for doing heavy topstitching, more decorative effects. 30 weight is just thick enough to give a little bit more of a difference.
So again, for topstitching and things. I do use cotton thread, but I tend to use it for more decorative elements, like decorative stitching, rather than construction work. Now of course there are many different kinds of specialty threads, but cotton and polyester are the most common. But there is, believe it or not, you can buy silk thread. Now, I'm not sure why this seems so odd, because back in the day, wasn't that long ago, silk was the thread that you used for almost everything.
And this white thread is actually 100 weight. It's very, very fine. If you choose to sew with silk thread, be aware that it is of course biodegradable which means it also, too, will potentially break down over time. Silk thread is UV sensitive, you don't want this to be exposed to sunlight for long periods of time. It will rot.
And that could be potentially unfortunate. So, you keep your silk thread covered, or you keep it in a drawer or a box or something so it's out of the sunlight. You just always want to keep it out of the light. Your silk thread, if you store it. So we have 100 weight here, we have, I believe this is quilter's silk, so this is, I believe, this may even be 10 weight.
I think it's even heavier than 12 weight. It's like 10 or maybe even eight. I don't think it says on my spool. But my spool is mostly in Japanese so it's hard to tell, but, I believe this is a 10 weight. So when I compare it to the cotton 12 weight, you can see it's considerably, it's heavier than that.
So this may even be a 10 or an eight. It's a very heavy silk thread. So you need a size, going back to our needles, I use a size 100 needle, for this silk thread. Just to make sure that there's a big enough hole to pass it through the fabric without shredding the thread. Okay, now, this is more of a regular sewing weight.
This is a 50 weight. So here we have three different weights of thread. We've got 100 weight, 50 weight, and then what I think it said eight or 10. Quite heavy. There's also a lot of threads that we use, just for fun, basically.
And especially the metallics. So, there's different types of metallic threads, now, some metallic threads are not truly metallic. This one's called a Polystar and this Polystar has a, basically more of a polyester thread with sparkles in it. So it has some sparkly elements spun into the yarn, but the majority of, and yes, yarn and thread can be used interchangeably at times. But the thread, the sparkles are actually spun into the thread, and, it's slightly less abrasive to your sewing machine than an actual full-blown metallic.
So, one thing you have to be aware of with some of these threads, like cotton tends to lint your machines. Metallic tends to be very abrasive. And you have to bear this in mind, most people don't use enough metallic thread often enough to damage their machine over time, but you know, theoretically, if you did it enough it could, potentially, wear some grooves, or be hard on your tension discs. That being said, I use a lot of metallics, so I think it's worth the little extra wear and tear. This is just another, this is more of a true metallic, this is blue, and again it has just a little bit more abrasiveness to it, than the Polystar, that just has sparkles mixed in.
Now these other threads are actually plastic. So these are called Holoshimmer, or Sliver. And it says metallic, but it's not so much metal, as I said, it's a reflective plastic. And these are the most difficult to sew with. Not every sewing machine is going to handle these successfully.
You have to just try it and see. Some of the newer sewing machines have thread handling capabilities, that allow them to measure out the thread rather than drag it through tension discs. And that really helps for sewing with these. These also are very sensitive to heat. So, I find when I machine embroider with these, my machines will use these just fine, but I find that I can only embroider at a higher speed for about 15 minutes before my needle gets too hot and I have to let it cool down or else it'll start melting the thread.
Which makes it break. So we even have plastic threads. Now on kind of the opposite side of the spectrum, this is called Filaine, this is actually an acrylic blend of thread, I wanna say yarn, it kinda is a yarn, but we technically use it as thread. And this, again, is at least a 12 weight. The Filaine.
And this is for doing topstitching and embroidery effects, so decorative stitching effects. When you want the look of hand sewing. So similar to how you would use a cotton 12 weight but in this case it looks more like wool. So it looks more like crewel work, or something similar. So it's a big, big world of both needles and threads out there.
And I hope that you will just have fun with it, and explore it. So remember the important thing is, number one, match up the type of needle, that is, you know, whether it's denim or embroidery or whatever, to the type of sewing you're doing with the kind of fabric, match up the size of the needle to the size of thread you're using, and of course, the type of fabric you're using as well. So if you need to have a strong needle, you need to have a bigger needle. Or if you're using really fine fabric you can go with a finer, smaller needle. And when it comes to working with thread, it's really a matter of personal preference.
So again, don't be afraid to play around, just make sure you're using the correct needle for the type of thread that you're using.
Share tips, start a discussion or ask other students a question. If you have a question for the instructor, please click here.
Already a member? Sign in
No Responses to “14-Day Learn to Sew Series - Needles and Thread”